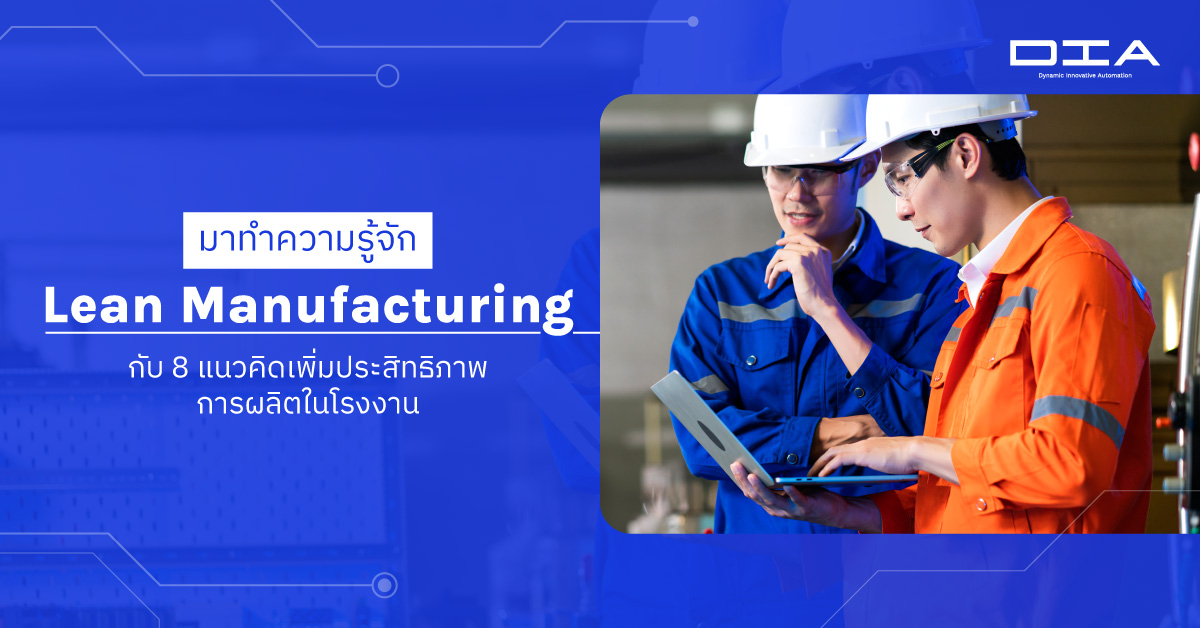
คำว่า ลีน (Lean) ถือเป็นคำที่หลายคนอาจคุ้นหู คุ้นตากันดี เนื่องจากถูกนำไปใช้ในหลากหลายบริบท ไม่ว่าจะเป็นด้านอาหารการกิน การออกกำลังกาย ธุรกิจ อุตสาหกรรม หรือแม้แต่การบริหารจัดการองค์กร ซึ่งลีนที่เราจะมาพูดถึงกันในวันนี้ คือ ระบบการผลิตแบบลีน (Lean Manufacturing) หรือรูปแบบหนึ่งของการผลิตที่ใช้กันมาอย่างยาวนานในวงการอุตสาหกรรม ทั้งโลกตะวันออก และโลกตะวันตก แต่ในประเทศไทยเอง อาจเป็นเรื่องที่ใหม่ หรือมีหลายองค์กร ทั้งภาคธุรกิจ และอุตสาหกรรมที่ต่างเริ่มสนใจระบบการผลิตแบบลีนมากขึ้น
ทาง dIA จึงอยากชวนทุกคนมาทำความรู้จักว่า ระบบการผลิตแบบลีน (Lean Management) คืออะไร มีที่มาจากไหน มีแนวคิดอย่างไร รวมถึงมีหลักการที่จะช่วยให้การผลิตในภาคธุรกิจ และอุตสาหกรรมดีขึ้นได้บ้าง
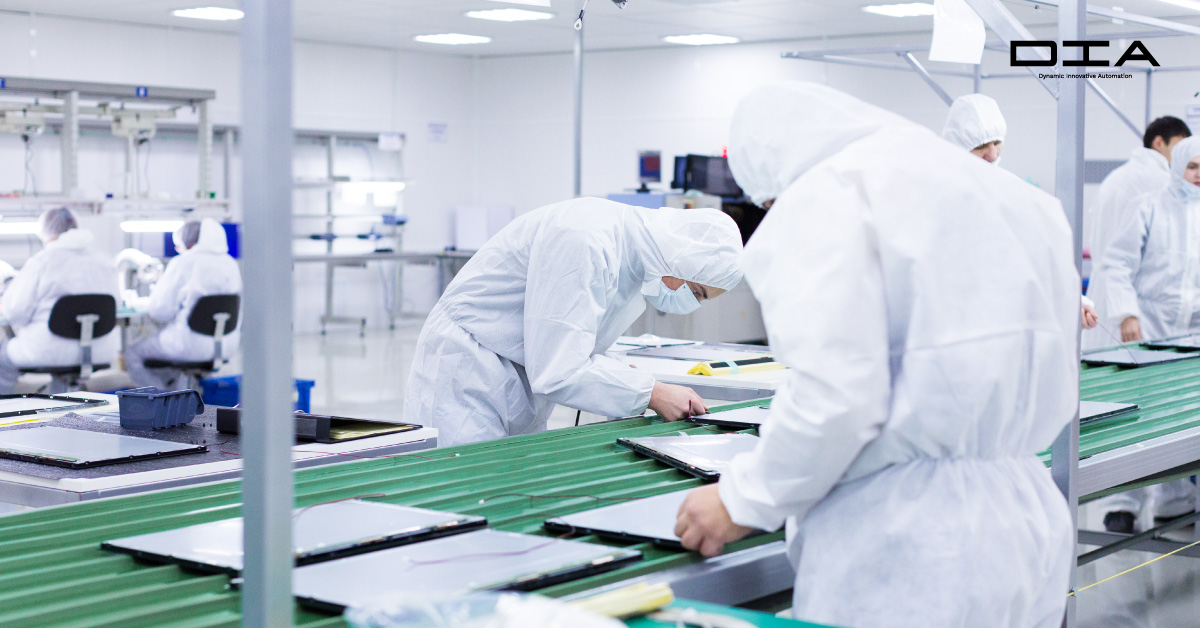
Lean Manufacturing คืออะไร มีที่มาจากไหน?
Lean Manufacturing คือ กระบวนการผลิต หรือแนวคิดที่มุ่งเน้นการเพิ่มประสิทธิภาพสูงสุดในการผลิต โดยลดความสูญเปล่า หรือกระบวนการทำงานที่ไม่จำเป็นออกไป รวมถึงการลดต้นทุน ทรัพยากร และระยะเวลาในการผลิต ในขณะเดียวกันก็มุ่งสร้างสรรค์ผลิตภัณฑ์ให้มีคุณภาพดี และมีคุณค่ามากยิ่งขึ้น
ระบบการผลิตแบบลีน (Lean Management) คือ ระบบที่มีต้นกำเนิดมาจากประเทศญี่ปุ่น โดย เออิจิ โทโยดะ (Eiji Toyoda) อดีตประธานบริษัท Toyota Motor คนที่ 6 ผู้พลิกโฉมหน้าระบบการผลิตของบริษัทโตโยต้า หลังจากได้ศึกษาดูงานจากบริษัท Ford ในรัฐมิชิแกน สหรัฐอเมริกา เขาได้ทำการพัฒนาระบบการผลิตแบบลีน จนได้ชื่อว่าเป็นผู้ให้กำเนิด “วิถีแห่งโตโยต้า” ซึ่งเป็นกระบวนการผลิตที่มีประสิทธิภาพ จนได้รับการยอมรับจากอุตสาหกรรมการผลิตรถยนต์ไปทั่วโลก
ในปัจจุบัน ไม่ได้มีเพียงแค่บริษัทโตโยต้าเท่านั้นที่ใช้ระบบการผลิตแบบลีน แต่หลายบริษัทในหลากหลายอุตสาหกรรมต่างก็ใช้ระบบการผลิตดังกล่าวเป็นแนวทางปฏิบัติขององค์กร เช่น Intel และ Nike รวมถึงบริษัทอื่นๆ อีกมากมายนับไม่ถ้วน ถือว่าเป็นระบบการผลิตที่มีอิทธิพลอย่างลึกซึ้งต่อแนวคิดการผลิตของอุตสาหกรรมต่างๆ อย่างปฏิเสธไม่ได้
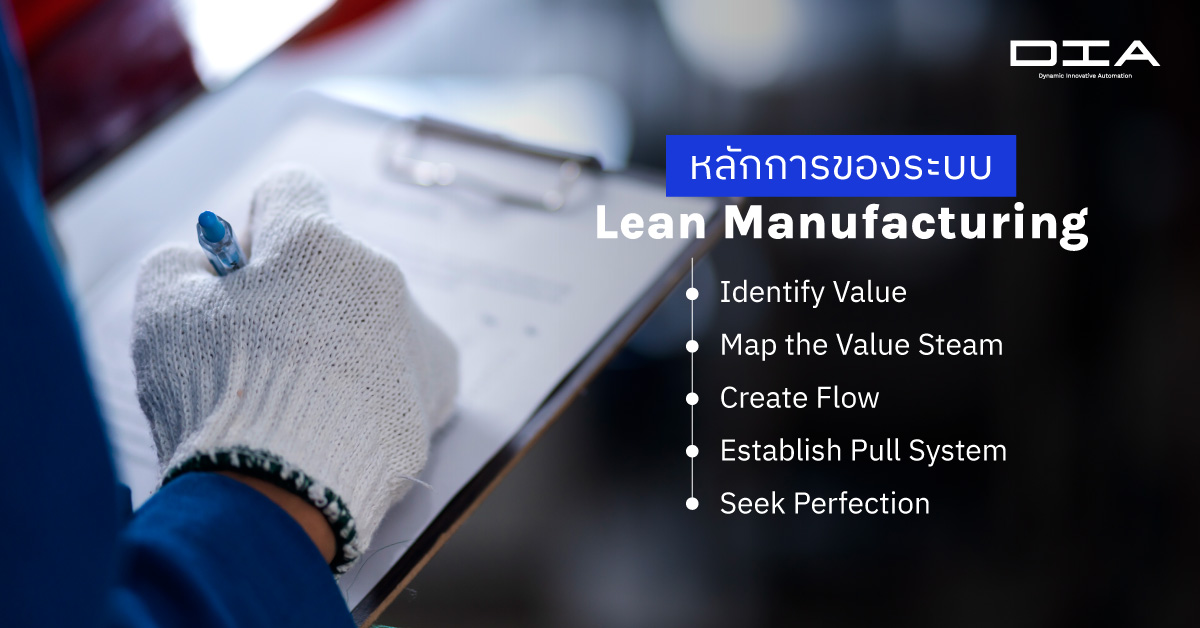
หลักการของระบบ Lean Manufacturing
ระบบการผลิตแบบลีน (Lean Manufacturing) มีแนวคิดพื้นฐานมีอยู่ 3 ประการ ได้แก่
- การมุ่งเน้นสร้างคุณค่าให้กับลูกค้า (Create Value)
- การลดความสูญเปล่าในกระบวนการผลิต (Eliminate Waste)
- การพัฒนาปรับปรุงกระบวนการทำงานให้ดียิ่งขึ้นไป (Continous Improvement)
โดยแนวคิด 3 ประการนี้ ได้กลายเป็นหลักการ 5 ข้อ ที่เป็นองค์ประกอบของระบบการผลิตแบบลีน ดังต่อไปนี้
1. การกำหนดคุณค่า (Identify Value)
การสร้างคุณค่า คือ สิ่งแรกที่ผู้ผลิตควรคำนึงถึงก่อนจะเปลี่ยนมาเป็นระบบการผลิตแบบลีน ซึ่งการสร้างคุณค่าต้องมาจากมุมมอง หรือความต้องการของลูกค้า กล่าวคือ บริษัทต่างๆ ต้องเข้าใจว่าลูกค้าต้องการอะไร ลูกค้ามีปัญหา หรือ pain point อะไร ตลอดจนการกำจัดบางสิ่งที่ไม่จำเป็นต่อความต้องการของลูกค้า เพื่อดำเนินการสร้างคุณค่าเหล่านั้นให้กับผลิตภัณฑ์ และบริการของตนเองให้ตอบโจทย์ลูกค้ามากที่สุด
2. การวางแผนการดำเนินงาน (Map the Value Steam)
ขั้นตอนต่อมา คือ การวิเคราะห์และวางแผนการดำเนินงาน รวมถึงกระบวนการการผลิตทั้งหมด หรือเป็นการสร้างวงจรของผลิตภัณฑ์ เช่น ขั้นตอนการออกแบบผลิตภัณฑ์ วัสดุ อุปกรณ์ ทรัพยากรที่ต้องใช้ แหล่งที่มา และที่ไปของสินค้า เมื่อวิเคราะห์กระบวนการที่เป็นวงจรเหล่านี้อย่างละเอียดดีแล้ว ก็จะสามารถลดขั้นตอน กระบวนการ หรือสิ่งที่ไม่จำเป็นออกไปได้
3. การสร้างขั้นตอนการทำงานให้ลื่นไหล (Create Flow)
การสร้างขั้นตอนการทำงานให้ลื่นไหล คือ หลังจากวางแผนการดำเนินงาน และกระบวนการผลิตแล้ว การนำเอามาปรับใช้ให้มีความลื่นไหล มีประสิทธิภาพ และพัฒนาได้อย่างต่อเนื่องเป็นสิ่งสำคัญ โดยถ้ากระบวนการผลิตต้องสามารถผลิตได้ตลอดเวลา หากเป็นกรณีที่ต้องมีการเคลื่อนย้ายการผลิต หรือสินค้า ระบบการขนส่งก็ต้องมีความลื่นไหล หรือต้องมีการคำนึงถึงทุกปัจจัยที่เกี่ยวข้องกับการผลิต ตลอดจนควรจัดสรรบุคลากรอย่างเป็นระบบ เพื่อให้ระยะเวลาในการผลิต ขนาดสินค้าคงคลัง และกระบวนการที่ไม่จำเป็นลดลง
4. การสร้างระบบดึง (Establish Pull System)
หลักการข้อที่สี่ การใช้ระบบดึง คือ การนำเอาความต้องการของลูกค้า หรือกลุ่มเป้าหมายมาเป็นหลักในการผลิตสินค้า เพื่อลดการผลิตแบบสิ้นเปลือง ลดการผลิตที่มากเกินไป หรือน้อยจนกินไป ลดปัญหาสินค้าคงคลัง และปรับกระบวนการทำงานให้สอดคล้องกับเป้าหมาย
5. การมุ่งสู่ความสมบูรณ์ (Seek Perfection)
หลักการข้อสุดท้าย คือ การปรับปรุงและพัฒนากระบวนการผลิต เพื่อมุ่งสู่ความสมบูรณ์แบบที่หลายบริษัทต้องการ แม้ว่าการแสวงหาความสมบูรณ์แบบ อาจดูเป็นคำที่ตรงไปตรงมา แต่ยังถือเป็นหลักการที่ยากที่สุดประการหนึ่งในการนำไปใช้จริงให้ประสบความสำเร็จ ดังนั้น สิ่งที่ทำได้คือการวิเคราะห์ผลสำเร็จจากการปฏิบัติตามหลักการข้อต่างๆ ที่ผ่านมา จากนั้นหาแนวทางในการปรับปรุง และพัฒนาตัวเองอย่างต่อเนื่อง เพื่อให้ผลลัพธ์ที่มีประสิทธิภาพอย่างยั่งยืน
แนวคิดความสูญเปล่า 8 ประการ
ก่อนอื่นชวนมาทำความเข้าใจก่อนว่า ความสูญเปล่า (Waste) ในทางธุรกิจหรืออุตสาหกรรม คือ สิ่งที่ไม่ได้สร้างคุณค่า หรือประโยชน์ให้กับลูกค้า ตั้งแต่ค่าใช้จ่าย วัสดุ อุปกรณ์ แรงงาน กระบวนการผลิต หรือการลงทุนที่ไม่มีความจำเป็น ซึ่งระบบการผลิตแบบลีน (Lean Manufacturing) คือ ระบบการผลิตที่มีจุดประสงค์เพื่อขจัดความสูญเปล่าเหล่านั้นออกจากกระบวนการทำงาน หรือกระบวนการผลิต
องค์ความรู้ หรือแนวคิดความสูญเปล่านี้ ได้รับการพัฒนาโดย ไทอิจิ โอโนะ (Thaiichi Ohno) ผู้ที่เคยเป็นหัวหน้าวิศวกรของบริษัทโตโยต้า โดยในช่วงแรกแนวคิดนี้มีทั้งหมด 7 ประการ (Toyota Production System – TPS) ได้แก่ การขนส่ง (Transpotation) สินค้าคงคลัง (Inventory) การเคลื่อนไหว (Motion) การรอคอย (Waiting) การผลิตที่มากเกินไป (Overproduction) กระบวนการส่วนเกิน (Over-Processing) และข้อบกพร่อง (Defects) หรือ TIMWOOD
แต่ภายหลังที่ระบบการผลิตแบบโตโยต้าถูกนำไปใช้ในโลกตะวันตก ในปี 1990 จึงได้มีการเพิ่มแนวคิดความสูญเปล่าข้อที่ 8 หรือ การใช้ทรัพยากรบุคคลได้อย่างไม่เต็มประสิทธิภาพ (Non-Utilize Talent) เข้ามา จนกลายเป็น 8 ความสูญเปล่าของระบบลีน (8 Waste of Lean) หรือ TIMWOODS นั่นเอง
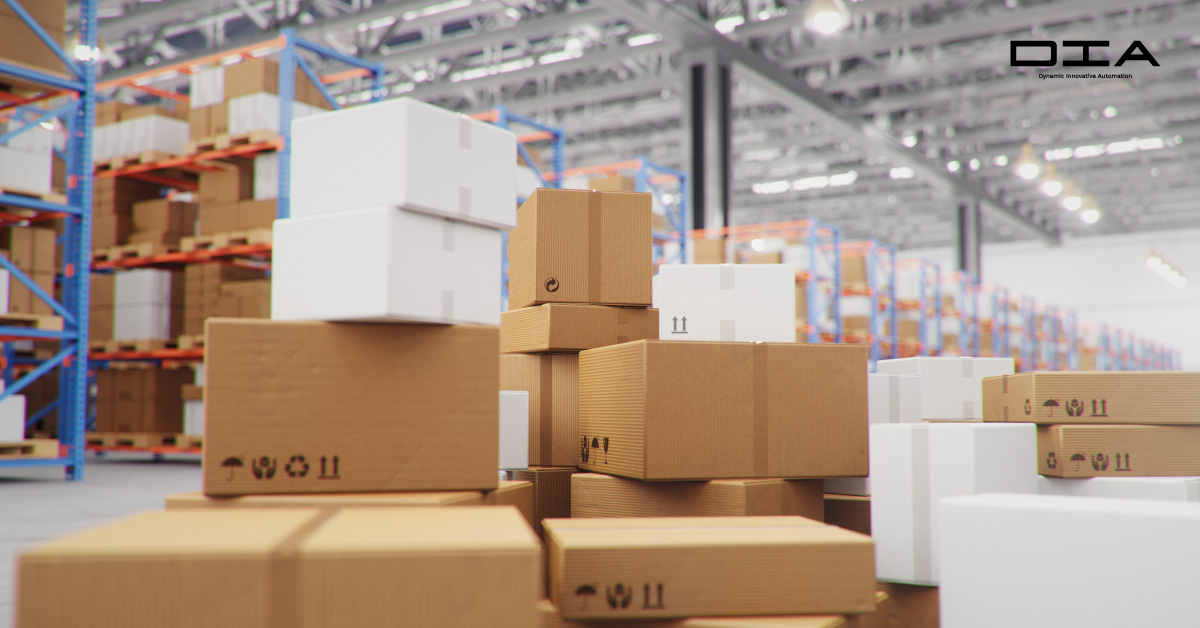
1. การขนส่ง (Transportation)
การขนส่งถือเป็นความสูญเปล่า เพราะหากมีการขนส่งหรือเคลื่อนย้ายวัสดุ เครื่องจักร แรงงาน และสินค้าอย่างไม่มีประสิทธิภาพมากเกินไป อาจทำให้ผลิตภัณฑ์ชำรุด และเสียหาย หรือแม้แต่การเคลื่อนย้ายวัสดุ อุปกรณ์ และแรงงาน ซึ่งทำให้เกิดการสึกหรอของอุปกรณ์ รวมถึงเกิดความเหนื่อยล้าเกินความจำเป็น สิ่งเหล่านี้อาจนำไปสู่ความสูญเปล่าอื่นๆ เช่น เกิดการรอคอยที่ไม่ก่อประโยชน์ใดๆ ให้กับองค์กร และกระบวนการผลิตสินค้า ดังนั้น วิธีการแก้ไขควรเริ่มต้นที่การออกแบบผังของโรงงาน ออฟฟิศ หรือกระบวนการขนส่งใหม่ เพื่อให้การทำงานมีประสิทธิภาพมากขึ้น
2. สินค้าคงคลัง (Inventory)
สินค้าคงคลัง อาจมองว่าเป็นได้ทั้งสินทรัพย์ และเป็นสินค้าส่วนเกินที่ถือเป็นความสูญเสียได้เช่นกัน ซึ่งส่วนใหญ่แล้วสินค้าคงคลังที่มากเกินความจำเป็น สามารถนำไปสู่ปัญหาต่างๆ ตามมาได้ เช่น การเก็บรักษาและดูแล โดยเฉพาะสินค้าหรือวัสดุที่พร้อมขาย ทำให้มีการใช้จ่ายที่ไม่จำเป็นไปกับการเก็บรักษาสินค้าเหล่านี้ โดยปัญหาสินค้าคงคลังเกิดจากการไม่คำนึงถึงปริมาณการจัดซื้อวัตถุดิบ รวมถึงการวางแผนที่ผิดพลาดของปริมาณการสั่งซื้อสินค้า ดังนั้น จึงควรมีการวางแผนการจัดซื้อ และการผลิตในปริมาณที่จำเป็นอย่างรอบคอบ เพื่อลดช่องว่างระหว่างการผลิต รวมถึงการป้องกันการผลิตที่เกินความจำเป็น
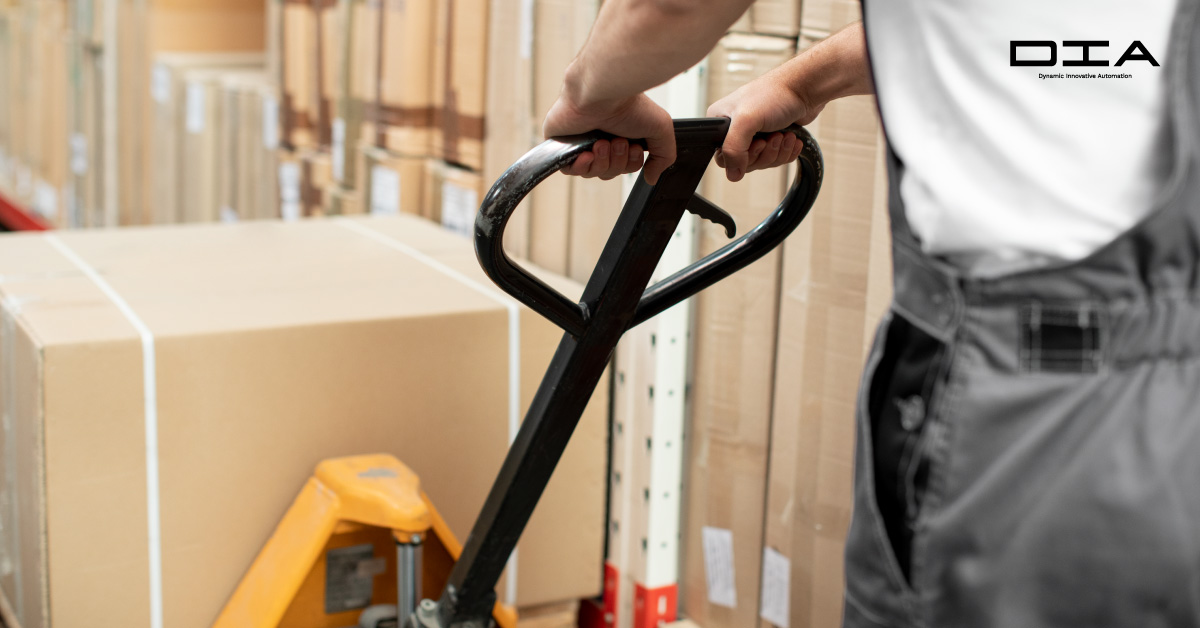
3. การเคลื่อนไหว (Motion)
การเคลื่อนไหว คือ ความสูญเปล่าที่ไม่ได้เกิดจากวัตถุดิบที่ใช้ในการผลิต แต่จะเน้นไปที่การทำงานของคน ร่วมกับอุปกรณ์ หรือเครื่องจักร โดยการเคลื่อนไหว หมายถึง การเดิน การยกของ การเอื้อม การหันไปมา การระบุตัวตนหลายรอบ การเคลื่อนไหวของเครื่องจักร เครื่องมือในการผลิต เป็นต้น ซึ่งการเคลื่อนไหวที่มากเกินไป ควรได้รับการออกแบบใหม่ เพื่อปรับปรุงการทำงานของบุคลากร เพิ่มระดับความปลอดภัย และใส่ใจสุขภาพ รวมถึงลดความสูญเปล่าจากการเคลื่อนไหวที่มากเกินความจำเป็น
4. การรอคอย (Waiting)
การรอคอย คือ ความสูญเปล่าประการหนึ่งที่สำคัญ อาจเกิดจากการรอคอยวัสดุ หรืออุปกรณ์ การรอที่เกิดจากความไม่สม่ำเสมอในการผลิต ทำให้ส่งผลเสียตามมา เช่น การมีสินค้าคงคลัง และการผลิตที่มากเกินไป นอกจากนี้ การรอคอยยังรวมไปถึงการรอการตอบกลับอีเมล์ รอเอกสารที่ต้องตรวจสอบ การประชุมที่ไม่มีประสิทธิภาพ รอคำแนะนำที่เหมาะสมก่อนการผลิต และการมีกำลังผลิตที่ไม่เพียงพอ ทั้งในแง่ของคน และเครื่องจักร การรอคอยเหล่านี้ไม่ได้ส่งผลดี และก่อประโยชน์ให้แก่บริษัท หรือองค์กร โดยปัญหานี้ มักเกิดจากการออกแบบกระบวนการทำงานที่ไม่มีประสิทธิภาพ
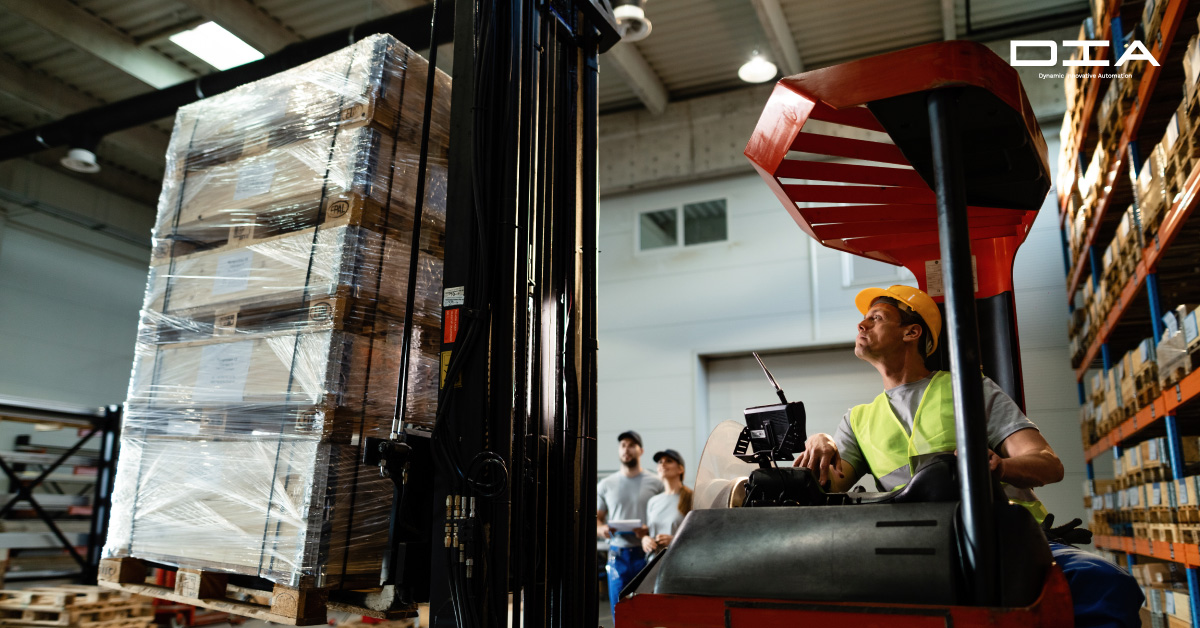
5. การผลิตที่มากเกินไป (Overproduction)
การผลิตที่มากเกินไป คือ การผลิตสินค้า หรือชิ้นส่วนประกอบของผลิตภัณฑ์ในจำนวนมากเกินความต้องการของกระบวนการทำงานในขั้นตอนต่อๆ ไป รวมถึงการผลิตที่มากเกินความต้องการของตลาด หรือลูกค้ากลุ่มเป้าหมาย ส่งผลให้เกิดความสูญเปล่าของทรัพยากร ทุน เวลา และขั้นตอนต่างๆ ในกระบวนการผลิต สินค้าที่ผลิตก็ไม่ได้สร้างคุณค่า หรือประโยชน์ให้แก่องค์กร เนื่องจากลูกค้าไม่ต้องการซื้อ ดังนั้น การควบคุมปริมาณการผลิตด้วยการคำนึงถึงความต้องการของลูกค้าจึงเป็นสิ่งสำคัญ
6. กระบวนการส่วนเกิน (Over-Processing)
ความสูญเปล่าข้อสุดท้าย แม้จะไม่ได้เป็นส่วนหนึ่งของระบบการผลิตแบบโตโยต้า (Toyota Production System – TPS) แต่ถือเป็นความสูญเปล่าที่มีความสำคัญ โดยเกิดจากการบริหารจัดการทรัพยากรบุคคลที่องค์กรส่วนใหญ่มักแยกบทบาทของผู้บริหารออกจากพนักงาน ทำให้หน้าที่การวางแผน การจัดระเบียบ ควบคุม และสร้างสรรค์กระบวนการผลิตตกอยู่ที่ฝ่ายบริหาร ในขณะที่พนักงาน คือ คนที่ปฏิบัติตามคำสั่ง และแผนงานที่ถูกวางเอาไว้
การไม่นำเอาบุคลากรที่มีความรู้ หรือเชี่ยวชาญในฐานะผู้ปฏิบัติงานแนวหน้าเข้ามามีส่วนร่วมในการพัฒนา ออกแบบ และวางแผนกระบวนการผลิต จึงเป็นเรื่องยากที่จะปรับปรุงกระบวนการทำงานให้มีประสิทธิภาพ ตลอดจนการอบรบบุคคลากรที่ไม่เพียงพอ การไม่มีแรงจูงใจ และการไม่ขอความเห็นจากพนักงาน ทำให้พนักงานหลายคนอยู่ในตำแหน่งที่ต่ำกว่าทักษะ ความสามารถ หรือคุณสมบัติที่มี พนักงานจึงไม่ได้แสดงศักยภาพอย่างเต็มที่ นอกจากนี้ ยังรวมถึงการมอบหมายงานให้พนักงานอย่างไม่เหมาะสมอีกด้วย
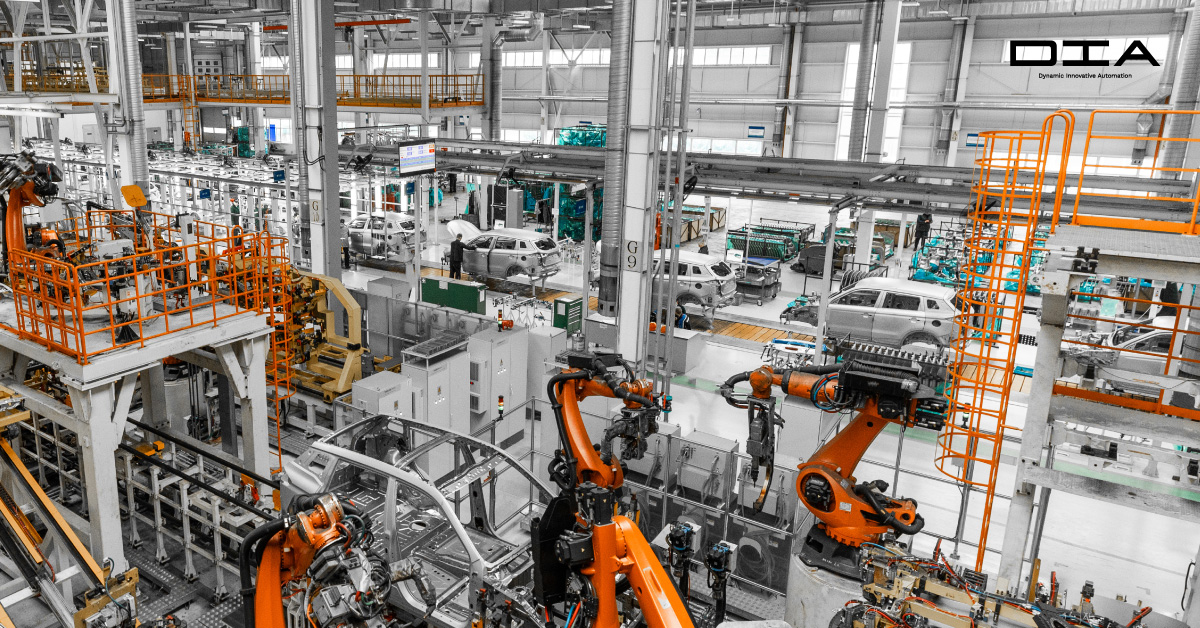
7. ข้อบกพร่อง (Defects)
ข้อบกพร่อง คือ การผลิตสินค้า หรือผลิตภัณฑ์ที่ไม่เหมาะสมกับการใช้งาน กล่าวคือ เป็นสินค้าที่ไม่มีคุณภาพ ส่งผลให้เกิดการผลิตซ้ำ แก้ไข หรือการทำลายผลิตภัณฑ์ทิ้งโดยเปล่าประโยชน์ ตลอดจนไม่ได้สร้างคุณค่า และประโยชน์ใดๆ ให้แก่ลูกค้า ตัวอย่างเช่น การผลิตสินค้าที่มีคุณภาพต่ำกว่ามาตรฐาน และถูกส่งผ่านไปยังมือของลูกค้า สิ่งนี้ถือเป็นความสูญเปล่า เนื่องจากส่งผลต่อความพึงพอใจของลูกค้าโดยตรง หากลูกค้ามีการนำสินค้าเข้ามาเคลม ทางบริษัทก็ต้องสูญเสียทั้งเวลา การขนส่ง แรงงาน และทรัพยากร
8. การใช้ทรัพยากรบุคคลได้อย่างไม่เต็มประสิทธิภาพ (Non-Utilize Talent)
ความสูญเปล่าข้อสุดท้าย แม้จะไม่ได้เป็นส่วนหนึ่งของระบบการผลิตแบบโตโยต้า (Toyota Production System – TPS) แต่ถือเป็นความสูญเปล่าที่มีความสำคัญ โดยเกิดจากการบริหารจัดการทรัพยากรบุคคลที่องค์กรส่วนใหญ่มักแยกบทบาทของผู้บริหารออกจากพนักงาน ทำให้หน้าที่การวางแผน การจัดระเบียบ ควบคุม และสร้างสรรค์กระบวนการผลิตตกอยู่ที่ฝ่ายบริหาร ในขณะที่พนักงาน คือ คนที่ปฏิบัติตามคำสั่ง และแผนงานที่ถูกวางเอาไว้
การไม่นำเอาบุคลากรที่มีความรู้ หรือเชี่ยวชาญในฐานะผู้ปฏิบัติงานแนวหน้าเข้ามามีส่วนร่วมในการพัฒนา ออกแบบ และวางแผนกระบวนการผลิต จึงเป็นเรื่องยากที่จะปรับปรุงกระบวนการทำงานให้มีประสิทธิภาพ ตลอดจนการอบรบบุคคลากรที่ไม่เพียงพอ การไม่มีแรงจูงใจ และการไม่ขอความเห็นจากพนักงาน ทำให้พนักงานหลายคนอยู่ในตำแหน่งที่ต่ำกว่าทักษะ ความสามารถ หรือคุณสมบัติที่มี พนักงานจึงไม่ได้แสดงศักยภาพอย่างเต็มที่ นอกจากนี้ ยังรวมถึงการมอบหมายงานให้พนักงานอย่างไม่เหมาะสมอีกด้วย
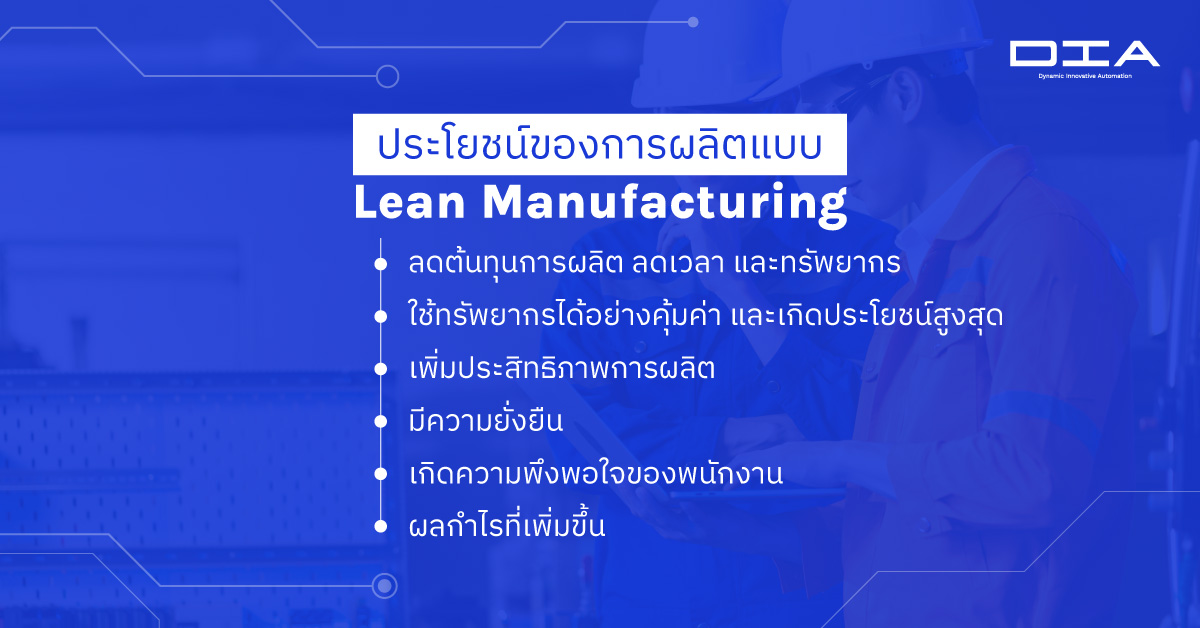
ประโยชน์ของการผลิตแบบ Lean Manufacturing
ประโยชน์ของระบบการผลิตแบบลีน (Lean Manufacturing) และแนวคิดแบบลีน 8 ประการ มีจุดประสงค์เพื่อลดหรือขจัดความสูญเปล่าเหล่านั้น เพื่อก่อให้เกิดประโยชน์และผลดีในระบบการผลิตของธุรกิจ และอุตสาหกรรม ดังนี้
- ลดต้นทุนการผลิต ลดเวลา และทรัพยากร เนื่องจากการลดความสูญเปล่าทั้ง 8 ประการ ถือเป็นการลดปัญหาด้านการผลิตต่างๆ ทั้งต้นทุน ทรัพยากร และระยะเวลา
- ใช้ทรัพยากรได้อย่างคุ้มค่า และเกิดประโยชน์สูงสุด เนื่องจากลดความสูญเปล่าในเรื่องการผลิตที่ไม่มีคุณภาพ การผลิตเกินความจำเป็น และการขนส่ง
- เพิ่มประสิทธิภาพการผลิต แน่นอนว่าการลดขั้นตอน และลดเวลาที่ไม่จำเป็น ย่อมส่งผลให้การผลิตมีประสิทธิภาพ ก่อให้เกิดประโยชน์และสามารถสร้างคุณค่าให้ทั้งลูกค้า และองค์กรได้
- มีความยั่งยืน เมื่อลดความสูญเปล่าลงได้ ก็เกิดความสามารถในการปรับตัวที่ดีขึ้นของธุรกิจ และอุตสาหกรรม ทำให้มีความพร้อมมากขึ้นเพื่อการเติบโตอย่างยั่งยืนในอนาคต
- เกิดความพึงพอใจของพนักงาน เนื่องจากพนักงานไม่ต้องทำงานที่มากเกินความจำเป็น ส่งผลให้กระบวนการทำงานมีความลื่นไหลมากขึ้น สร้างความพึงพอใจให้กับพนักงานได้
- ผลกำไรที่เพิ่มขึ้น แน่นอนเมื่อความสูญเปล่าลดลง ประสิทธิภาพการทำงาน และคุณภาพของผลิตภัณฑ์ที่ดีขึ้น ทั้งยังตอบโจทย์ความต้องการของลูกค้ากลุ่มเป้าหมาย และความต้องการของตลาด ส่งผลให้บริษัทมีกำไรมากขึ้นตามมาในที่สุด